By automating its supply chain quality and operational processes through the X1 platform, Raley’s was able to more efficiently:
- Take a risk-based approach to brand-specific requirements and processes that is adaptable, repeatable, structured, and streamlined
- Vet & manage private label suppliers—creating stronger, more trust-worthy relationships with clear and concise communications and reduced work cycles
- Create a more autonomous, empowering work environment for employees & supply chain partners
- Minimize risk and speed the execution of product withdrawals & recalls
opportunity
As a third-generation, family-owned American grocer, Raley’s is dedicated to nourishing its communities and carrying out its mission of “changing the way the world eats, one plate at a time.”
With that goal in mind, Raley’s partnered with CMX1 in January 2020 to automate many of their manual processes through the X1 platform, and create efficiencies and process consistency across the brand’s 200+ locations.
By establishing operational excellence, particularly with its growing private label offerings, Raley’s had the unique opportunity to create an exclusive, quality product—driving brand loyalty, repeat business, and business outcomes.
action
Raley’s focused on three key areas and established an action plan for each:
supplier management
To help its team be more efficient and consistent in its approach to working with private label suppliers, Raley’s took a series of steps that provided more visibility and control over those supplier relationships. This included leveraging the X1 platform to:
- Automate questionnaires & the collection of related documents that help their team evaluate potential suppliers including production locations & capabilities, food safety practices, product certifications, and facility audits
- Create a streamlined & expedited approval process that requires little to no communication outside the X1 platform
- Establish clear expectations customized to specific types of vendors and product types, creating uniformity across the business and ensuring “all boxes are checked”
- Implement state and FDA-specific regulations automatically
product lifecycle management
To improve quality management, Raley’s utilized the X1 platform to more efficiently create, control, and track its private label product specifications including quality, packaging, and labeling requirements. With more than 3,000 items housed within its three private labels (Raley’s, organic Raley’s Purely Made, and premier Nob Hill Trading Co.), the grocery brand was able to more quickly and thoroughly address customer questions about products (e.g., ingredients, allergens, animal welfare) and respond to customer inquiries escalated by its retail service center.
recall management
Nothing can negatively impact a grocery brand more than a mishandled recall. Understanding every minute counts, Raley’s implemented X1’s recall management solution, providing the brand with the automated tools necessary to quickly initiate a withdrawal or recall event, promptly launch a mitigation plan, and ultimately, better protect its customers.
The automated system allowed any Raley’s QA team member to initiate a withdrawal or recall —helping the brand identify impacted locations more quickly, communicate with those stores directly, expedite a more prompt resolution, and reduce unnecessary food waste and costs.
outcomes
Raley’s efforts have yielded many positive results. Employees are engaged with the X1 platform, collaborating across internal departments and with suppliers, and using real-time reporting to drive continuous improvement—establishing KPIs, identifying risk, and measuring ongoing performance. Additionally, the company has made tangible improvements by integrating its supplier, product, and recall management into one streamlined platform.
supplier management
- More complete profiles and a deeper understanding of its supplier partners, their performance, & overall compliance
- Increased engagement and positive feedback from vendors impressed by the X1 platform & its ease of use
- Faster vetting and approval process of suppliers, decreasing complete process to 2-3 weeks (vs. several months with previous process)
product lifecycle management
- Streamlined and automated workflows for the creation, collaboration, review, & approval of private label product specifications
- Increased speed to market with quicker approval of new products
- Faster response times for customer inquiries regarding private label products
recall management
- 85% of recalls are closed within 2 hours or less (a 45-ppt improvement with CMX1 vs. previous process)
- Positive environmental impact with no paper footprint and less waste
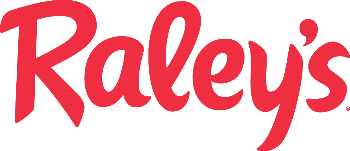
what's next
With its continued focus on operational and quality excellence, Raley’s plans to implement ActivitiesX1 to develop and execute automated programs, both in-store and within their supply chain. Plans include temperature checks and monitoring of in-store refrigeration across locations, as well as enabling quality assurance team members to automate internal audits when visiting manufacturing plants of supplier partners.