3,600+ Drive-Ins | 500+ Products | 100+ Suppliers | 30+ Distributors
SONIC, America’s Drive-In is the nation’s largest drive-in restaurant chain serving approximately 3 million customers every day. Ninety-five percent of SONIC’s more than 3,600 drive-ins are owned by local business men and women. For 65 years, SONIC has delighted guests with signature menu items, 1.3 million drink combinations and friendly service by iconic Carhops.
SONIC is part of the Inspire Brands family of restaurants.
opportunity
Prior to working with CMX, Sonic had come to a crossroads. Like so many other fast-growing brands, they had identified gaps and operational inefficiencies in their supply chain. Their QA team was stretched thin.
- Should we add more headcount or invest in improving our systems?
- What can we afford?
- Can we afford not to?
The team faced several challenges:
Diverse menu with many partners = Complexity
Sonic has the most diverse menu in QSR made up of more than 500 products sourced from more than 100 suppliers, through 30+ Distributors.
Inflexible and siloed systems
Sonic had separate systems with pockets of information in each but no single consolidated view of their partners, products, and quality data, making it challenging to get work done.
Too many manual processes
The QA Team was working to maintain this information in too many systems and tackling tasks manually. This resulted in inconsistent information, delays in closing product related incidents, delays in credit/replacement processing for Drive-Ins, and labor intensive efforts to execute product withdrawals.
action
Sonic quickly reached the conclusion that adding more people was not the most effective way to address their challenges.
Prior to selecting the CMX1 platform, Sonic evaluated several “point solutions” in the market. Many lacked important functionality and offered little more than the ability to share documents.
What Sonic really needed was a data-driven solution that fit their budget and could be configured to meet their needs now and in the future. They needed a solution that automated key business processes and freed up their team to focus on what really matters.
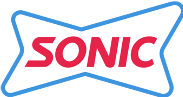
Sonic’s “Supply Chain Quality Management Portal” leverages the CMX1 platform in the following ways:
Supply Chain Relationship Management & Transparency
CMX1 provides a single source to view and manage all of Sonic’s Supplier, Distributor, Bakery, and Drive-Ins and relationship information. This includes all of the “hierarchy” relationships for Franchisees and “above restaurant” field management. CMX1 provides Sonic the ability to view, manage, and monitor their Product to Supplier, Supplier to Distributor, and Distributor to Drive-In relationships:
Product Specifications
Sonic uses CMX1’s attachment-based Product Specifications configuration as an alternative to the fully data-driven option. This option still provides all the visibility and control of the more robust option but keeps things simpler with shorter forms and workflows. Specifications include header information, product categorization, attachments and photos.
Crisis Management
Sonic also leverages the CMX1 platform to manage and resolve product related issues reported by their Drive-Ins and Distributors, and to automate and streamline the process for executing product holds, withdrawals and recalls.
Incident Management
Sonic uses CMX1 to automate the resolution and monitor trends for product-related complaints, quality, and delivery issues for their Drive-ins and supply chain partners.
- Automation: The module provides a simple, yet intelligent form for reporting issues that leverages all of the relationship data stored in the platform to automatically route cases. Drive-Ins simply input a Product ID, the issue, and desired resolution, and the system does the rest. Cases are automatically routed to the correct Distributor, Bakery, or Supplier depending on the issue type for resolution.
- The system has streamlined and automated the reporting, resolution, and credit/replacement process from days to hours.
- Monitoring: CMX1 automatically monitors trends and alerts the QA Team of possible systemic issues with particular products, distributors, or suppliers. Used along with CMX1’s Recall Management, the team can seamlessly transition to an investigation, and further response management if needed.
Recall Management
Sonic was a strategic partner of CMX's initial development of CMX1's Recall Management module.
Sonic leverages the module to conduct investigations and manage hold/release, withdrawal, and voluntary/mandatory recalls from initiation to resolution. It also gives the team the needed tools to execute “mock” events throughout the year.
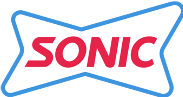
outcomes
The implementation of CMX1 has had a significant impact on Sonic’s ability to manage and monitor supply chain quality, risk and compliance as their business continues to grow rapidly.
The primary benefits include:
- Total Supply Chain Transparency: CMX1 provides the consolidation and integration of all their partner information, data and relationships across Suppliers, Distributors, Bakeries, Drive-Ins, Franchisees, and field hierarchy to give the QA Team a single system to view and proactively manage Sonic’s supply chain quality, risk and compliance focused programs.
- The “Crisis in “Crisis Management” has been significantly reduced: CMX1 provides Sonic the automation, monitoring, case management, and communication tools to resolve product related issues, withdrawals and recalls more effectively and efficiently.
- Operational Efficiency: CMX1 has dramatically improved Sonic’s supply chain quality by creating new operational efficiencies through process automation, integration with multiple data sources, improved record keeping, and insightful reporting. With CMX1, Sonic and its Franchisees are saving time, money and effort.
For more information and other Client Stories, please visit www.cmx1.com or call 1-858-866-8888.